
Pitch People: Restoring A 25-Year-Old Cinematic Documentary into 4K
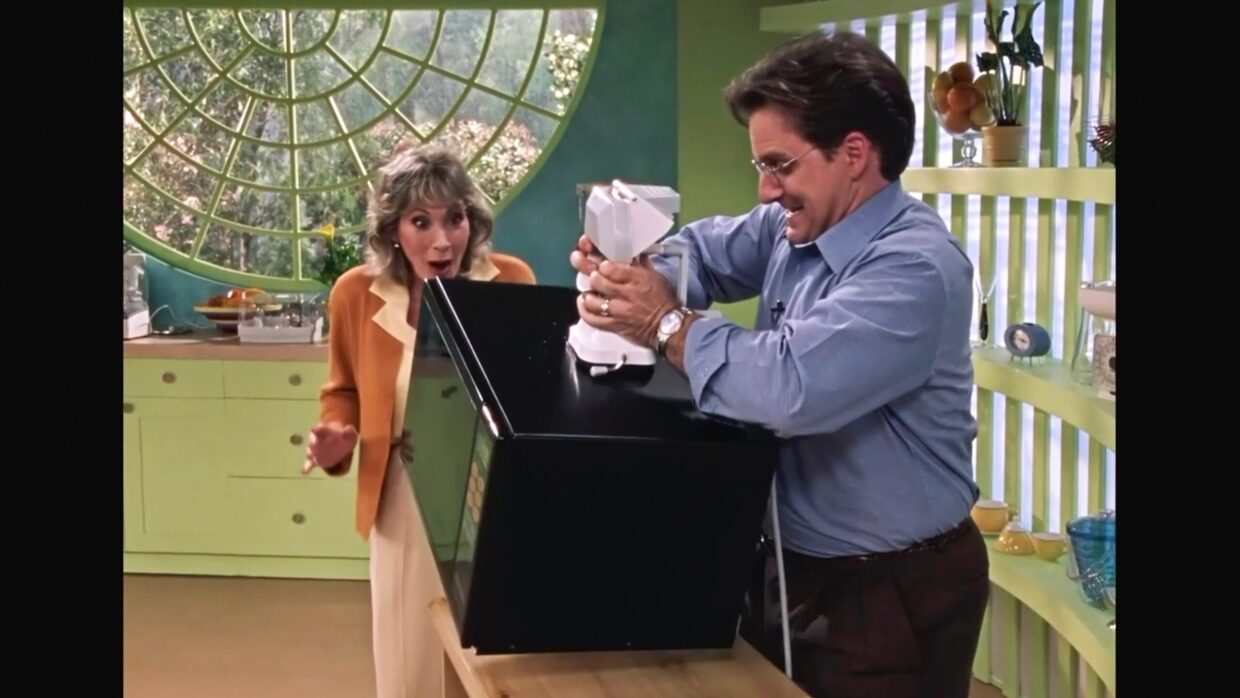
Pitch People is a feature documentary that takes an energetic look at the pitch business, a dynamic world that started in Europe, made its way to the U.S. boardwalks, and exploded on worldwide television in the 1990s. The film was completed in 1999. It was well-received at various festivals and independent film venues but a year later, it was still incomplete. It was missing an audience, partially due to it never having a formal theatrical release.
In 2020, production and postproduction stopped due to the pandemic. With advanced filmmaking tools available and new ways of making people aware of a film, I decided to restore the film and make it again available. The effort would utilize idle equipment and provide a project for some of the artists I’ve worked with over the years.
Shot On Film
The documentary was originally shot on Super 16mm film stock. Shooting with 16mm was less expensive than shooting on 35mm film. The camera equipment was also smaller, making it ideal on a documentary production that had many set-ups and locations. Super 16mm utilizes 20 percent more of the film surface in a 1.66 aspect ratio than regular 16mm, giving you more image and less grain in a 35mm blow-up. The film stocks we used were Kodak Vision 7245 (50D), 7246 (250D), 7248 (100T), 7274 (200T), 7277 (320T), 7279 (500T) and some footage on Fuji 8651 (250T) due to Kodak film being out of stock one day.
A New Way to Edit / Conforming the Negative
In the late 1990s, electronic editing systems were replacing film-based machines like the Moviola and flatbed editors. Software was available that correlated the edit made on a 29.97 fps electronic system with the key numbers on the 24fps film. We cut the film on an electronic system and once it was locked, the edit decision list (EDL) was converted to a negative cut list and given to the negative cutter.
Before I describe what happened during the restoration, a bit of the film postproduction process needs to be explained.
When 16mm negative is cut together, to keep the splices invisible it is assembled into A/B rolls. The beginning and end of each shot is spliced to a piece of black film. Opposite that shot, on the “B” roll, is an equal length of black film followed by the next shot. The “A” roll has a piece of black film of equal length opposite the “B” roll shot and that process is repeated until the reel is made of two checkerboarded, frame-accurate rolls (A and B).
Since we planned to blow the film up to 35mm, A/B rolls needed to be created from a 35mm interpositive instead of the original 16mm neg. The negative cutter assembled all the 16mm shots (with six frame handles) into an A roll. That roll was then loaded into a liquid gate optical printer at the lab and blown up to 35mm. The blow up was then conformed into A/B rolls by the negative cutter. Since this was an interpositive and not a negative, the shots were checkerboarded with clear film between them instead of black film. A 35mm internegative would be created from these conformed interpositive A/B rolls and release prints struck from that.
Film Opticals
We had a lot of titles (opticals) to add to the film (people’s names, locations, etc.), and we didn’t want to take these specific shots for an extra generation because you can see a visual difference. To do this, we took the 35mm interpositive shots that needed an optical and made a 35mm internegative with the title. When that optical was cut into the 35mm internegative you wound up with all the shots being the same generation providing a consistent visual flow.
Scanning Surprise
Since the original film had been color corrected (timed) in the photochemical world, restoring the film from the interpositive would save time. Any new color work, in theory, would be minimal. I contacted Dino Everett at USC’s SCA Hugh H. Hefner Moving Picture Image Archive and brought him the interpositive rolls to scan into 5K dpx files from which we would restore the film.
During the scanning process, Dino discovered white, powdery residue falling from the film as it moved through the scanner. We stopped the scanning and I took the interpositive to FotoKem in Burbank, one of the few labs left still involved with photochemical work. They found the clear leader used between the shots in the interpositive, with time, had leeched into the picture areas irreparably damaging it. The damage varied, the worse being in the areas of the footage adjacent to the clear film.
At this point we had three choices. We could scan one of the 35mm release prints, scan the 35mm internegative (which was unharmed) or scan the original 16mm negative. We tested scans from each and found that the original 16mm contained the best resolution (since it hadn’t gone through an optical process) and offered a large range of available colors. The downside of using the 16mm was that the entire film would have to be assembled and colored again. We decided to scan the original 16mm negative and use the color in the original release print as a guide for the colorist to retime the film.
It was quite exhilarating seeing crip, dimensional images emerge in the 5K dpx scans, as if the film was shot last week. There was a lot clean-up to do since dirt really shows up on 16mm and had increased due to all the initial and new handling of the negative.
Other Film Damage
During production, shipping film in protective, lead-lined photographic bags had always been safe going through airports. When we looked at the footage we shot in England in April 1998, we discovered it was polluted with green and blue flashes that varied in intensity. We sent the footage to Kodak in Hollywood for investigation. They discovered it was x-ray damage and, on June 18, 1998, Kodak issued a warning about a new type of high-intensity x-ray scanner used at over 50 international airports.
In 1996, POP Film in Santa Monica was acclaimed for creating some of the visual effects in the feature, Independence Day. I did a lot of post work at their video division and asked if they had a way to remove the flashing from the shots. They determined it could be done, but the cost to repair all the affected shots added up to over $50,000. Our production insurance only provided $20,000 for film damage. We had them repaired as much as we could with that sum but several damaged shots still remained in the film.
Today, there are digital tools available that can repair footage at a fraction of the 1998 cost. All the x-ray damaged footage in the film has now been corrected thanks to Prasad Corporation.
Archive Footage Challenges
The archive footage in Pitch People came from a variety of sources and also presented challenges. In the late 1990s, many of the archive companies had their sources on videotape and most of the demand was for video-based productions, not film projects. Our policy was to always ask the archive house for original sources. If the shot originated on film, we asked them to track down the film element. We found many of the original film elements had been abandoned by the archive services and were no longer available.
The film was being remastered in 4K from the 5K film scans and we wanted to gently bring all the non-film sources up to this resolution. If an archive source only existed on videotape, we utilized software, such as Topez Video, to up-rez the footage. The sources were mainly supplied on Beta SP and Digital Beta videotape. Even the film elements that could be found had gone through many generations by the time they made it to the archive house and contained a lot of noise and grain or had fading in the color layers. Our goal was to moderately reduce the grain and noise but hold off if it looked too processed. We kept the original intended aspect ratio of all archive footage out of respect to the original camera people who shot it.
Final Assembly and Color
The entire film was assembled and conformed on a Flame workstation by Jon Van Wye. The colorist, Tim Vincent, worked in DolbyVision on Resolve with calibrated HDR and SDR monitors. The goal was to restore the theatrical experience provided by the original 35mm print and bring it in line with today’s advancements so it would also look great in homes. The restoration was a three-year process, the same amount of time it took to shoot the film in the late 1990s.
When I screened the DCP in preparation for the film’s theatrical re-release in 2024, it was very emotional. Seeing the pitch people again — alive, bigger than life — hearing their rat-a-tat patter, experiencing the expressive world in which they existed in vivid detail — it was all consuming. If viewers experience just a fraction of that, the restoration was well worth the time and effort.
During the entire process, a business story was always on my mind. After gaining control of MGM Studios, the management under investor Kirk Kerkorian sold off the studio’s props in 1970. Filmed screen tests and original nitrate prints were barged out to the Pacific Ocean and dumped. While those screen tests may have been of individuals who were never heard of again and the prints were films determined to be irrelevant by someone, they were an important record of the times. The way those individuals spoke, the way they dressed, the words they used, the way they looked — that was all sent to deteriorate at the bottom of the sea and made permanently unavailable to later generations of cultural scholars, storytellers and documentarians. This is why preservation and restoration should always be a part of the discussion.
Stanley Jacobs is the director, editor and producer of Pitch People. SJPL Films releases the restoration of Pitch People tomorrow, March 1, at New York’s Village East theater. Next Friday, March 8th, it will open in Los Angeles at the Lumiere Cinema and in Chicago at the Wayfarer Theater. It will then open Friday, March 15 at the Emagine Willow Creek in Minneapolis and the Cinelounge Tiburon in the San Francisco Bay Area.